Machines by Feige FILLING
Our portfolio of semi- and fully automatic equipment
Here we proudly present our comprehensive range of state-of-the-art machines that revolutionise efficiency and productivity in many lines of business. Immerse yourself in our varied range and discover the excellence Feige FILLING embodies in every product.
Safe filling with calibrated accuracy
A safe and clean filling process is of particular importance, especially when using machines in potentially explosive atmospheres. Our drum filling equipment complies with the most stringent requirements. The equipment is designed for drums ranging from 50 l to 230 l. Depending on your needs, you can choose between semi- or fully automatic equipment. All our equipment can be complemented with conveyor and palletising systems.
Semi-automatic
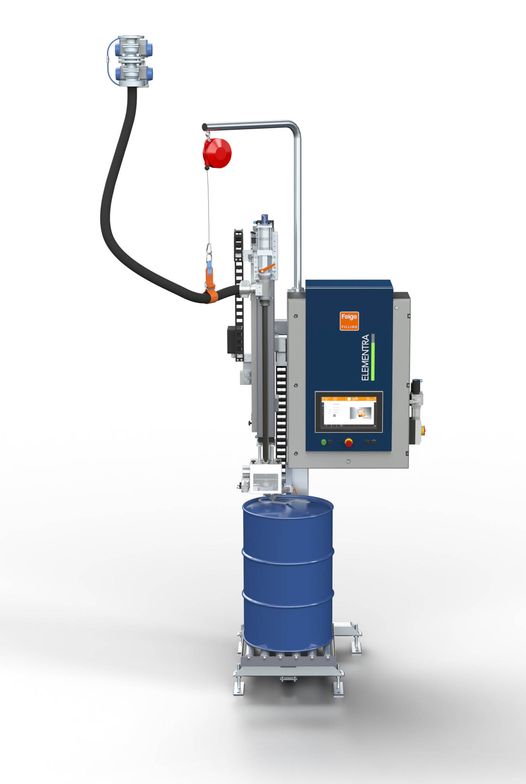
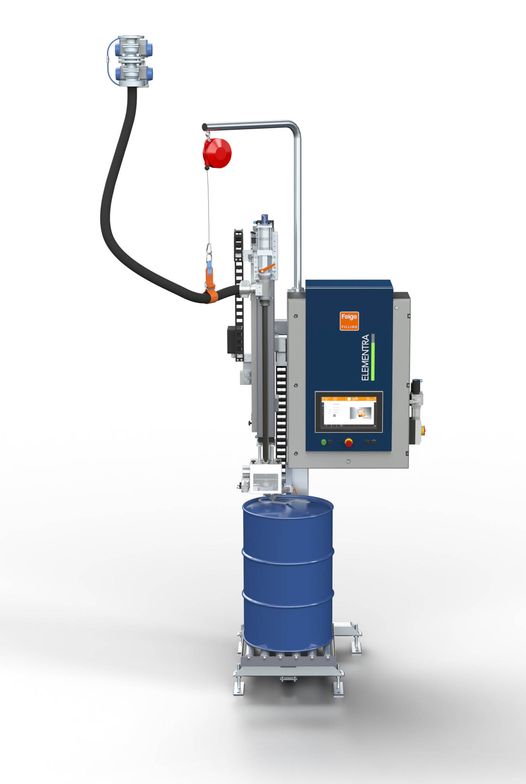
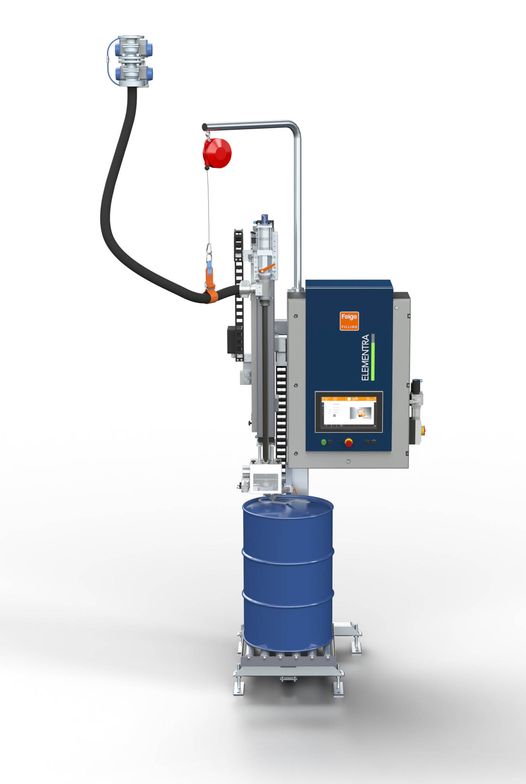
Our drum filling equipment ELEMENTRA® 29 forms the core of a state-of-the art filling line, complete with comprehensive conveyor system and additional peripherals. A NOVELTY are our fully electric designs, which require no compressed air and are thus particularly energy-efficient.The ELEMENTRA® 29 unites all functions of a gravimetric filling machine and is characterised by the well-proven FEIGE quality. We have integrated well-proven components from our FEIGE modular system, amongst others the pressure relieved filling valve with quick-action mount and a minimum of dead spaces. In addition, we offer important accessories such as controlled drip collecting, overflow message and gas extraction directly at the filling opening. During the filling operation, the drum is securely fixed on the weigh scale to ensure the highest precision. Manual offset screwdrivers and sealing devices with spring balancer suspension are available for opening and closing.
The benefits - drum filling equipment ELEMENTRA® 29
- Sturdy basic structure with machine feet for levelling
- Easy installation
- Easy operation
- Below- or with-surface filling with weight-controlled upward movement, below-bunghole filling or above-surface filling
- FEIGE web HMI as user interface with integrated scale display and operation monitoring
- More than 1000 dosing parameters for different products possible
- Control of on-site product pump or pilot valve is included
- Fully electro-mechanical scale base with 4 load cells by default in stainless steel design
- Any number of drive units can be controlled
- A driven roller conveyor is possible on the weigh scale platform
- The roller conveyor on the weigh scale at the same time serves as collecting basin
- Matching, complementary product hose with hose suspension available
- Stainless steel and acid-resistant design possible
- Mobile design optional
- ATEX design possible
Fully automatic
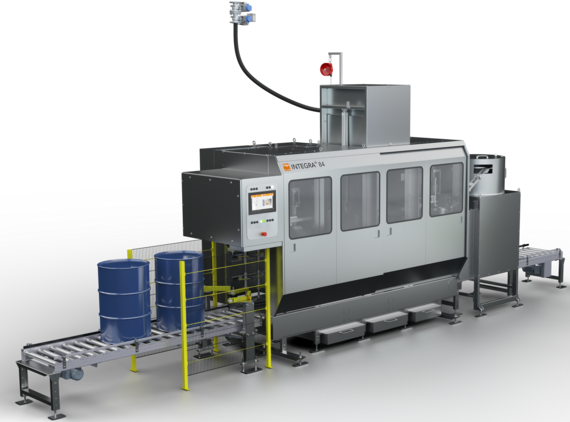
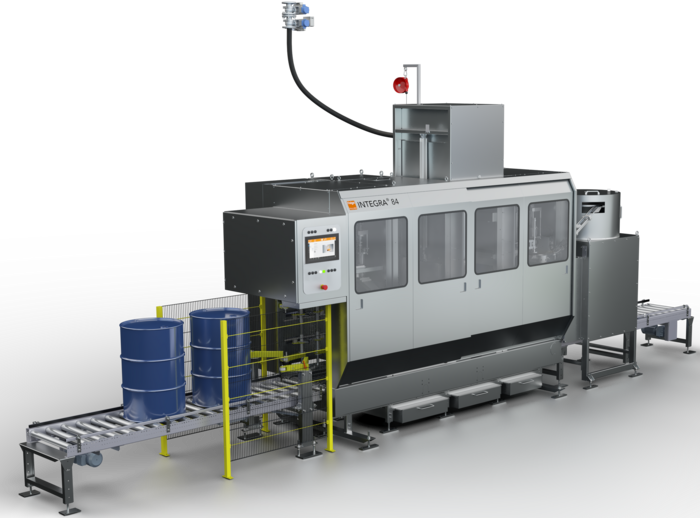
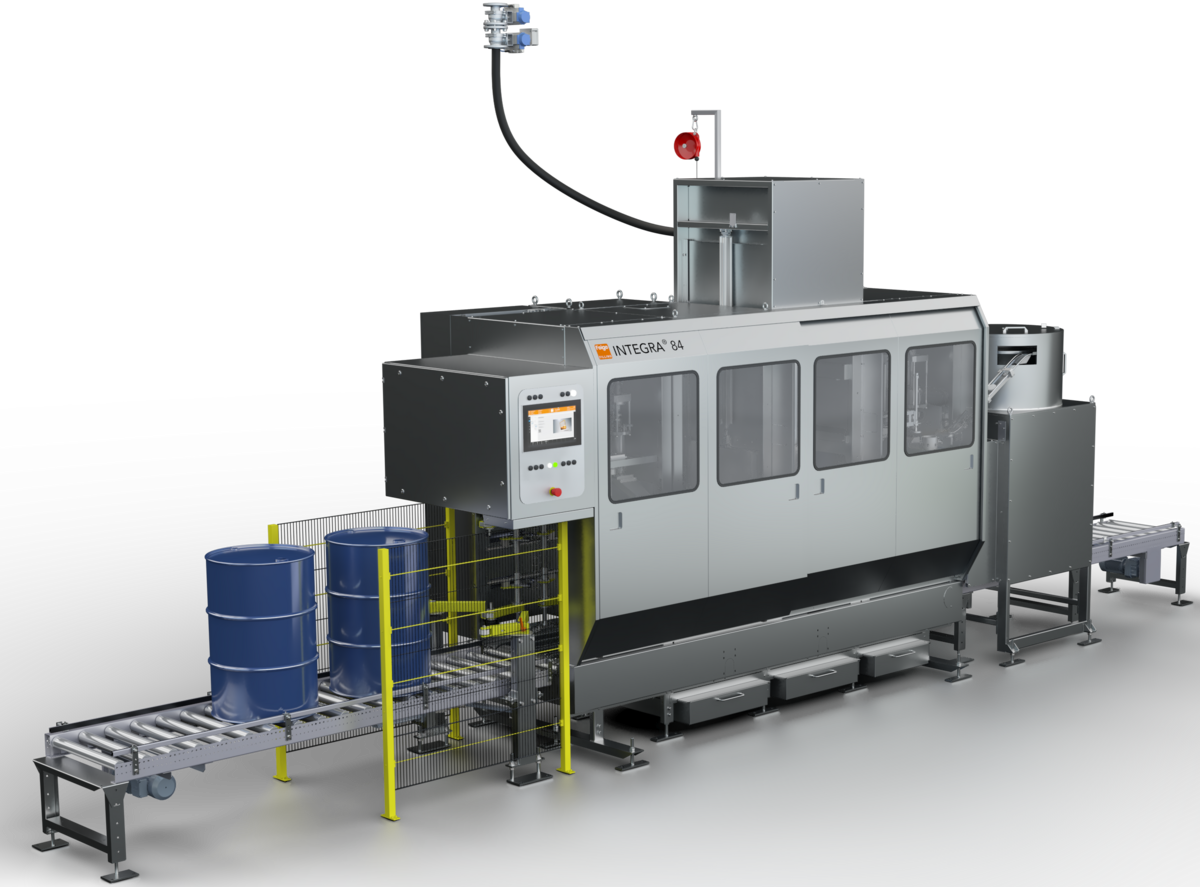
With our drum filler INTEGRA INTEGRA® 84 you optimise your filling processes and considerably increase your productivity per hour. This innovative machine is equipped with four stations for fully automatic and calibrated filling of bung-type drums. The drums are precisely transported through the machine by a chain conveyor in single cycle mode and are fed to the individual work stations. In the meantime, empty drums are automatically positioned and opened, while simultaneously, an already opened drum is filled in the filling station and a filled drum is reliably closed in the closing station. To further increase the performance, a pre-filling station can be integrated in the second cycle. This station transfers the tare weight to the final filling station and fills the drum in coarse fill mode, which further increases the efficiency of the entire process.
Your benefits - drum filler INTEGRA® 84
- Automatic opening, closing and sealing of standard closures with monitoring
- With accessories suitable for filling ISO steel drums and ISO plastic drums ranging from 50 l to 230 l
- Filling cabin can be executed as closed protection cabin with lock gate
- Stainless steel and acid resistant design possible
- With conveyor technology and other peripheral components extension to a filling line possible
- Option to connect to superordinate systems
- FEIGE web HMI as user interface with integrated scale display and operation monitoring
- More than 1000 dosing parameters for different products possible
- Tare check, flow rate control, dosing time monitoring
- Below- or with-surface filling with weight-controlled upward movement or below-bunghole filling
- Product hose with direct filling valve connection
- ATEX design possible
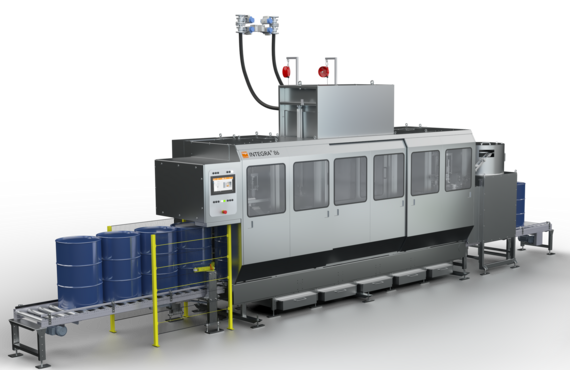
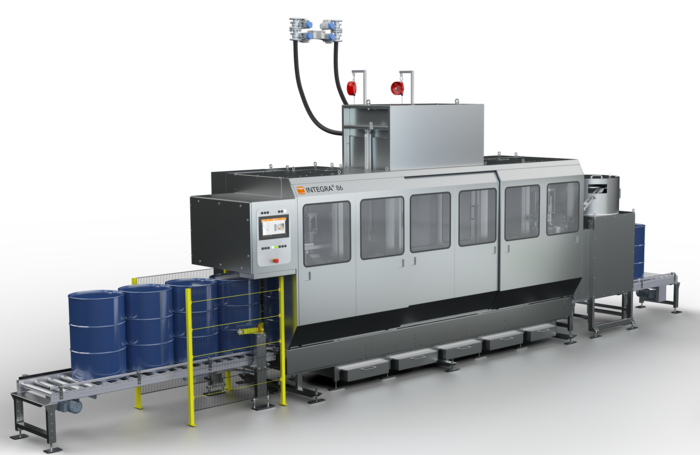
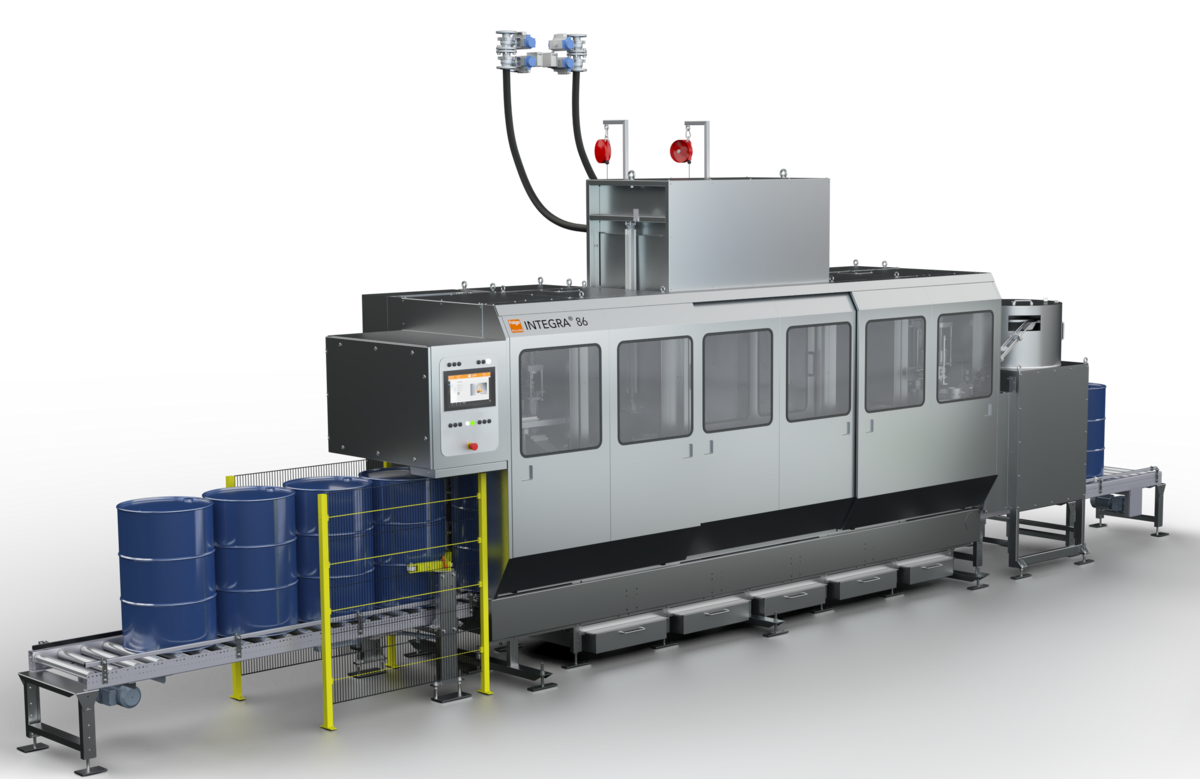
Our high speed drum filler INTEGRA® 86 with its six stations enable ultrafast filling of bung-type drums at maximum speed. The drums are alternately transported through the machine in double and single cycle mode by a chain conveyor and fed to the respective work stations. In a continuous process, the machine automatically positions and opens two empty drums in a row, while simultaneously two already open drums are filled at the same time in the filling stations. Afterwards, two filled drums are successively reliably closed in the closing station.
The INTEGRA® 86 thus not only offers high-performance filling, but also optimises the process flow through the simultaneous processing of several drums, thus clearly increasing the productivity and efficiency of your filling equipment.
The benefits - drum filler INTEGRA® 86
- Automatic opening, closing and sealing of standard closures with monitoring
- With accessories suitable for filling ISO steel drums and ISO plastic drums ranging from 50 l to 230 l
- Filling cabin can be executed as closed protection cabin with lock gate
- Stainless steel and acid resistant design possible
- With conveyor technology and other peripheral components extension to a filling line possible
- Option to connect to superordinate systems
- FEIGE web HMI as user interface with integrated scale display and operation monitoring
- More than 1000 dosing parameters for different products possible
- Tare check, flow rate control, dosing time monitoring
- Below- or with-surface filling with weight-controlled upward movement or below-bunghole filling
- Product hose with direct filling valve connection
- ATEX design possible
Our pallet filling equipment caters for different containers
Our semi- or fully automatic pallet fillers are suitable for containers ranging from 20 l to 1000 l. It is up to you to chose the degree of automation that matches your requirements. You can manually position the containers for the corresponding bunghole alignment or you can leave detection of the bunghole up to state-of-the-art camera technology. All systems can be extended with transport and packaging equipment.
Semi-automatic
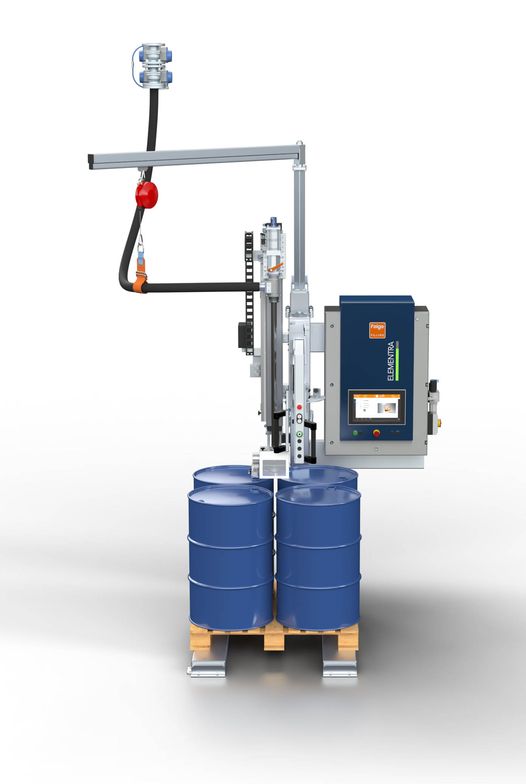
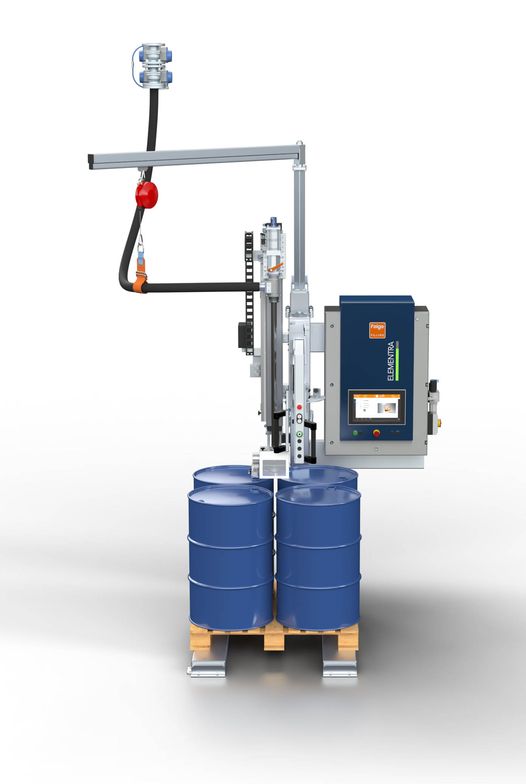
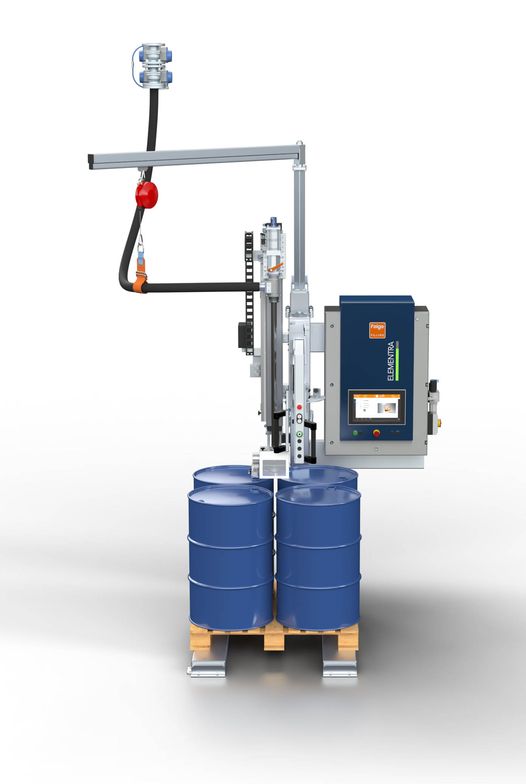
The solution to meet your needs “plug and fill”. The pre-configured pallet filling station ELEMENTRA® 16 for the semi-automatic filling of containers and drums arranged on pallets. The pre-configured pivoting pallet filling station offers you all the functions of a gravimetric filling machine with comprehensive product file.
Many well-proven components from the modular FEIGE system, such as the pressure relieved, minimum dead space filling valve in the quick-action mount, are used.
The benefits - pallet filling station ELEMENTRA® 16
- Cost-effective solution, the entire control and operation are located on the filling station
- Very flexible filling station, also suited for filling IBC up to a height of 1160 mm
- Short lead times because of pre-configured solutions
- Sturdy column design
- Rapid installation
- Easy operation
- Below-surface filling with weight-controlled upward movement, below-bunghole filling or above-surface filling
- FEIGE web HMI as user interface with integrated scale display and operation monitoring
- More than 1000 dosing parameter records for different products possible
- Control of on-site product pump or pilot valve is included
- Fully electro-mechanical scale base with stainless steel-load cells
- Up to 5 drive units can be controlled
- Also available with flip-open pit scale
- Matching, complementary product hose with hose suspension available
- Stainless steel and acid-resistant design possible
- Mobile design possible
- ATEX design possible
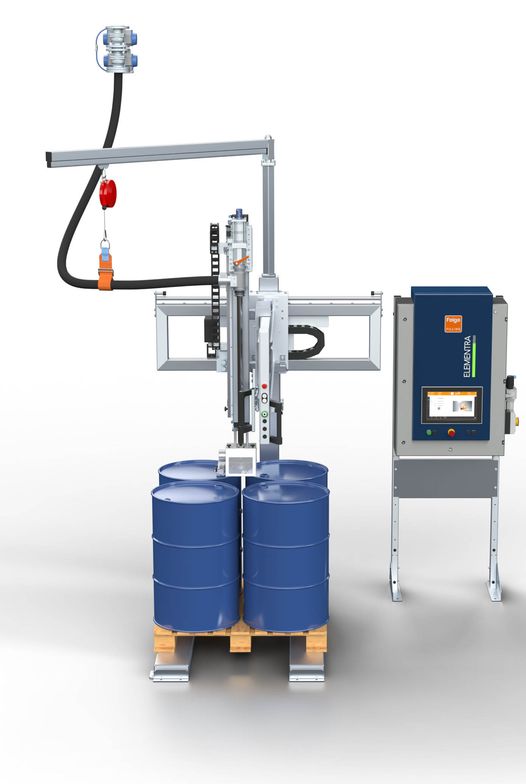
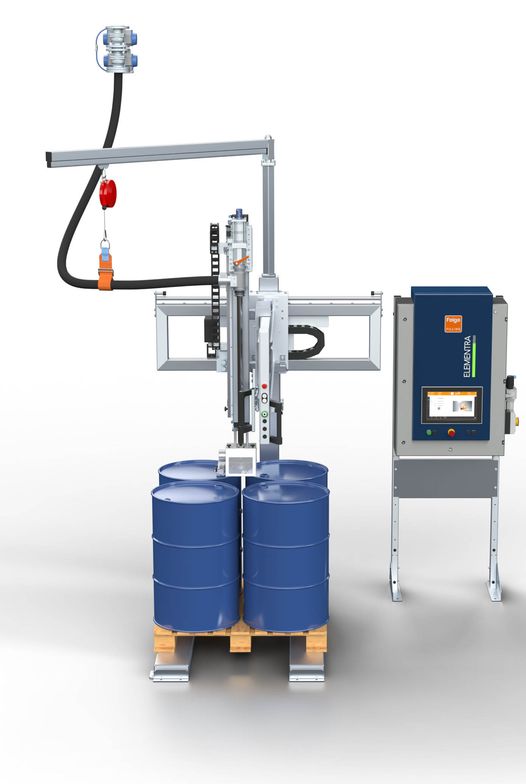
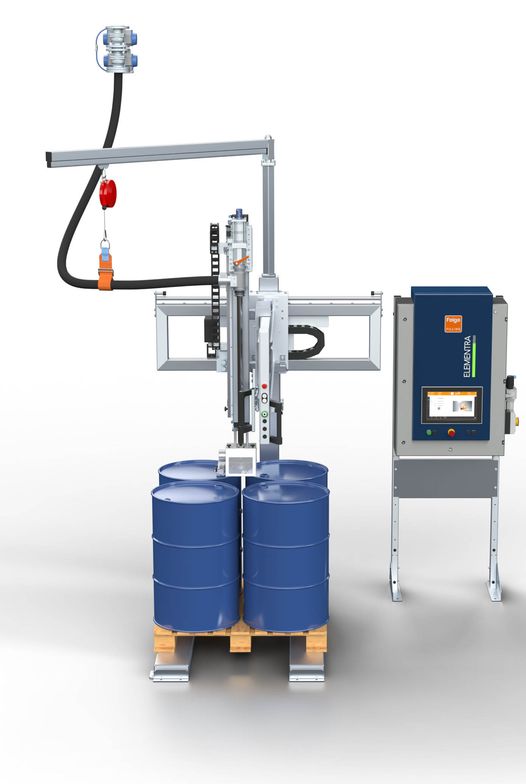
With the pre-configured pallet filling station ELEMENTRA® 17 that has been designed with you in mind you can rapidly and cost-efficiently solve your every demand. The extremely flexible “Plug + Fill” filling station is ideally suited if operation is to take place from the front only.
Optional system accessories allow for automatic or controlled drip collecting, overflow message or gas exhaust, also directly at the filling opening, inerting, a complementary product hose system und drain funnels.
The benefits - pallet filling station ELEMENTRA® 17
- Cost-effective solution, the entire control and operation are located on the filling station
- Very flexible filling station, also suited for filling IBC up to a height of 1350 mm
- Very well suited if operation can take place from the front only
- Short lead time because of pre-configured solutions
- Sturdy column design
- Rapid installation
- Easy operation
- Below-surface filling with weight-controlled upward movement, below-bunghole filling or above-surface filling
- FEIGE web HMI as user interface with integrated scale display and operation monitoring
- More than 1000 dosing parameters for different products possible
- Control of on-site product pump or pilot valve is included
- Fully electro-mechanical scale base with stainless steel-load cells
- Up to 5 drive units can be controlled
- Also available with flip-open open pit scale
- Matching, complementary product hose with hose suspension available
- Stainless steel and acid-resistant design possible
- Mobile design possible
- ATEX design possible
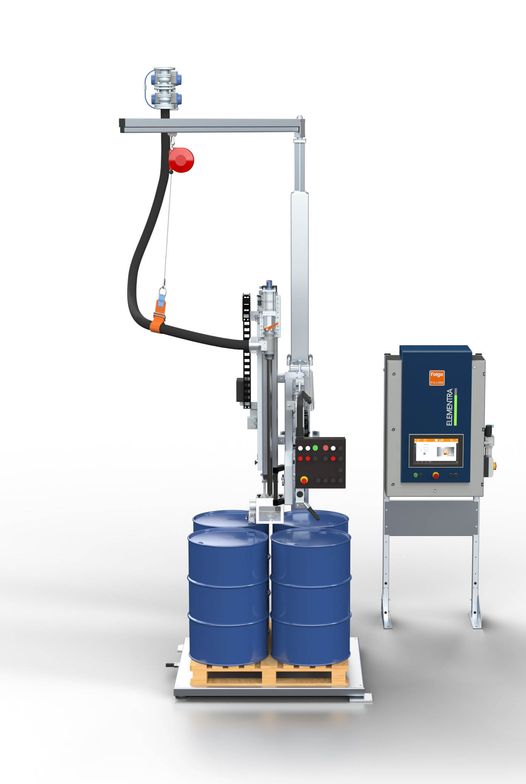
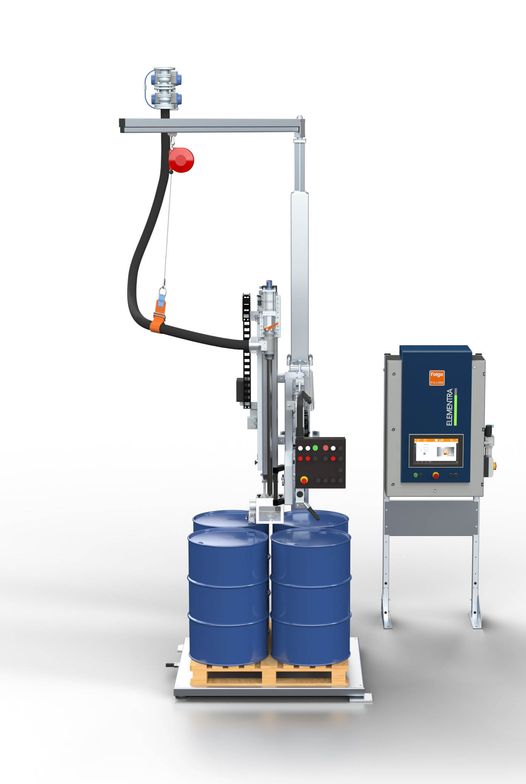
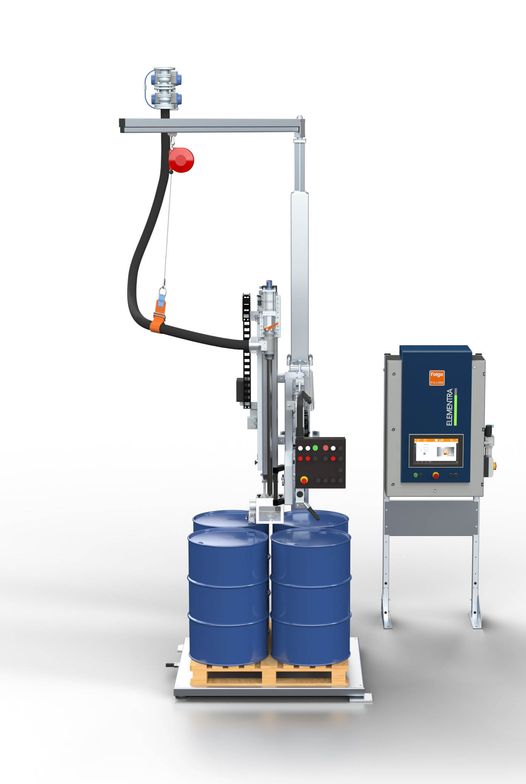
The pallet filling system ELEMENTRA® 26 provides you with a sound basic structure for the installation of a filling line with comprehensive conveyor system and further peripherals
As central component of your filling line, the pivoting pallet filling equipment can be extended with conveyor technology or other sub-assemblies at any time. Use the scalable nature of the pivoting equipment to your benefit and optimise your production processes entirely according to your ideas.
The benefits - pallet filling system ELEMENTRA® 26
- Very flexible filling system, also suited for filling IBC up to a height of 1550 mm
- Large area that can be reached with the filling valve
- Sturdy column design
- Extension to a filling line with conveyor technology and other peripheral components possible
- Below-surface filling with weight-controlled upward movement, below-bunghole filling or above-surface filling
- FEIGE web HMI as user interface with integrated scale display and operation monitoring
- More than 1000 dosing parameters for different products possible
- Control of on-site product pump or pilot valve is included
- Fully electro-mechanical scale base with stainless steel-load cells
- Any number of drive units can be controlled
- Also available with flip-open pit scale
- Matching, complementary product hose with hose suspension available
- Stainless steel and acid-resistant design possible
- ATEX design possible



The IBC filling equipment ELEMENTRA® 28 can be used as central component of your filling line with comprehensive conveyor system and further peripherals.
The ELEMENTRA® 28 is your first choice if you opt for an economic system consisting of standard components, sub-assemblies and control concepts, yet desire to obtain customised engineering to suit your individual requirements.
You use all the components and accessories in the usual FEIGE quality and are free to extend the equipment according to your own ideas.
The benefits - IBC filling equipment ELEMENTRA® 28
- Sturdy column design
- Below-surface filling with weight-controlled upward movement, below-bunghole filling or above-surface filling
- FEIGE web HMI as user interface with integrated scale display and operation monitoring
- More than 1000 dosing parameters for different products possible
- Control of on-site product pump or pilot valve is included
- Fully electro-mechanical scale base with stainless steel-load cells
- Any number of drive units can be controlled
- Also available with flip-open pit scale
- Matching, complementary product hose with hose suspension available
- Stainless steel and acid-resistant design possible
- ATEX design possible
Fully automatic
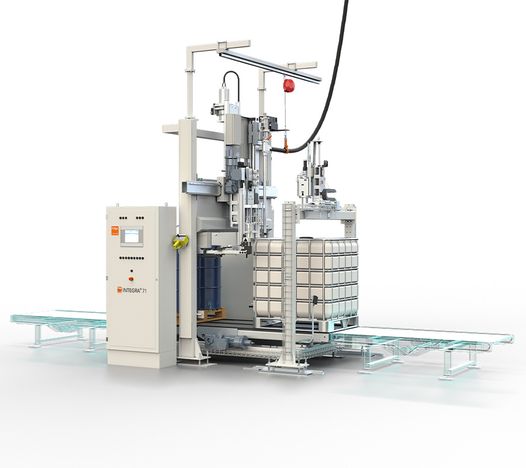
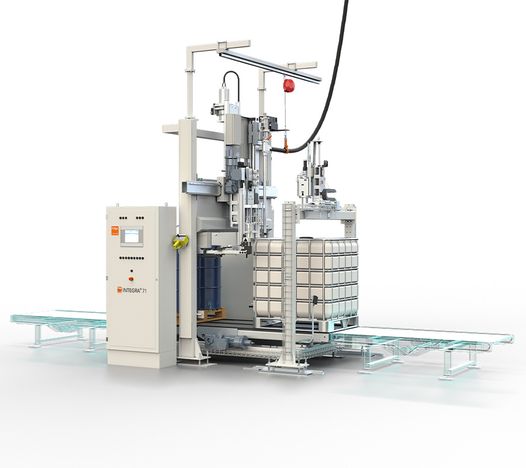
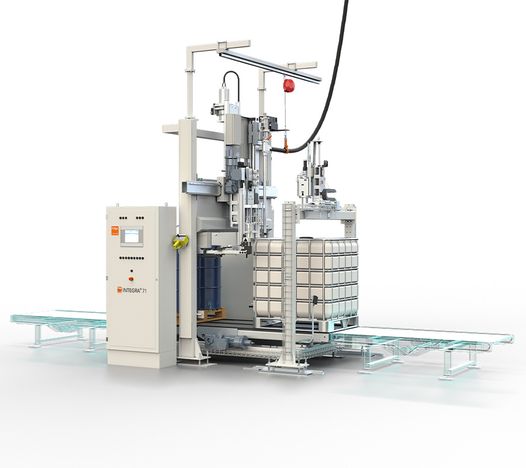
You aim to automate your filling processes? Then you should take a closer look at the gantry-type pallet filling robot INTEGRA® 7. The pallets move with empty containers across carrying chain conveyors onto the scale base. During their entry, a line scan camera scans the surface. It automatically detects the positions of the filling openings and checks the position of the openings for plausibility.
Subsequently, the containers are automatically opened, filled, closed and even sealed, if you wish.
Your benefits - gantry-type pallet filling robot INTEGRA® 71
- Extension into a filling line with conveyor technology and other peripheral components possible
- Fully automatic detection of filling openings and corresponding positioning
- Containers need not be pre-aligned
- Safe detection even of dirty or labelled surfaces
- Image correction possible after every filling
- Automatic base height adjustment of the entire machine to change over to different containers heights
- Filling of multiple layers and filling of incomplete pallets possible
- Reliable prevention of double filling
- Tare check, gross total check, flow rate control
- Dosing time monitoring
- More than 1000 dosing parameter records for different products possible
- Below-surface filling with weight-controlled upward movement
- FEIGE web HMI as control interface with integrated scale display and operation monitoring
- Possibility to connect to superordinate systems
- Stainless steel and acid-resistant design possible
- ATEX design possible
Semi-automatic and extensible
Our semi-automatic filling equipment ELEMENTRA® 24 processes up to 400 pails/h, depending on the product. The weighing ranges approved for verification range between 0.5 and 60 kg. This equipment forms the central component for extension into a filling line. Numerous accessories and comprehensive conveyor systems round off the process.
Niklas Gentes
![[Translate to English:] Niklas Gentes](/fileadmin/FeigeFilling/Mitarbeiterfotos/Niklas_Gentes.png)
Niklas Gentes
Sales Manager
Semi automatic
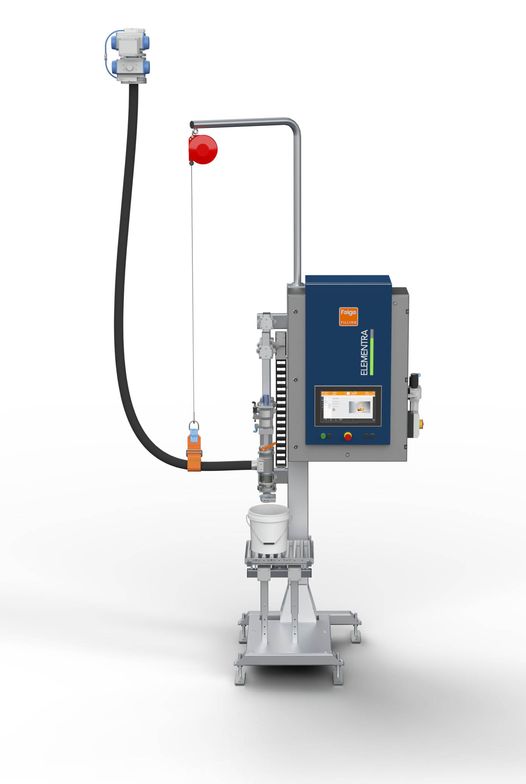
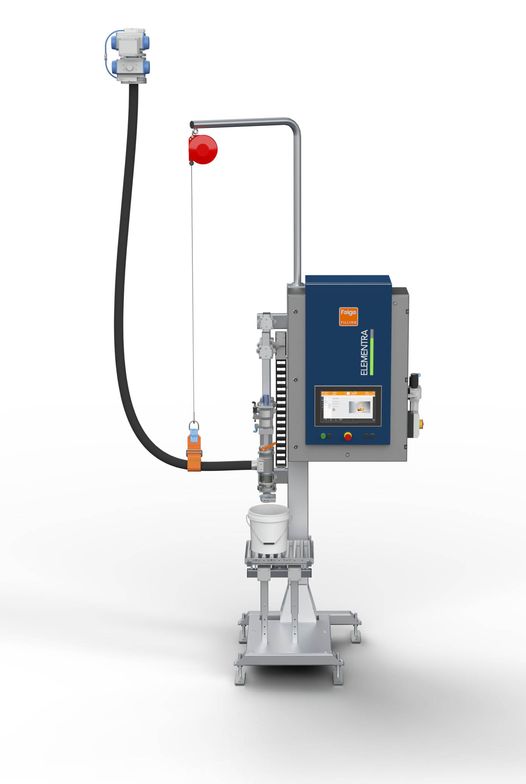
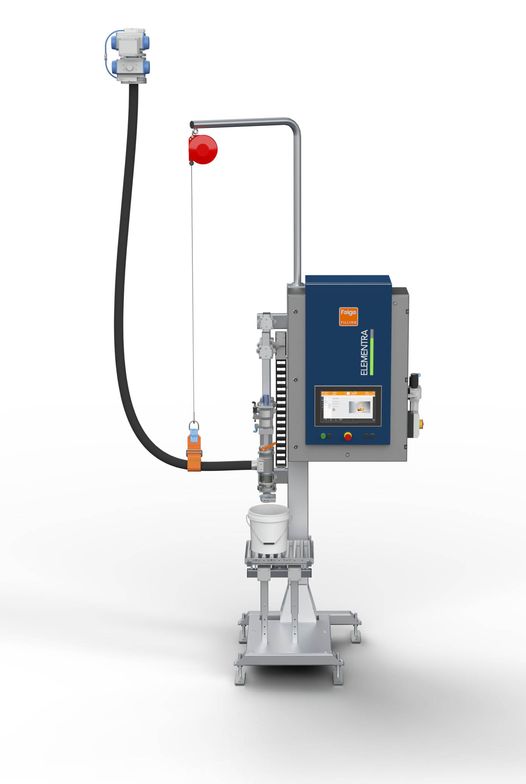
The sound basic structure of the pail filling equipment ELEMENTRA® 24 offers you the central component of a filling line with extensive conveyor system. Roller conveyors and further peripheral components for the in-feed and out-feed area permit a flexible extension of the system solution. To increase its performance, you can complement the pail filling equipment with a pail denester, lid magazine or palletising aid or palletising robot at any time.
The benefits - pail filling equipment ELEMENTRA® 24
- Sturdy basic structure with machine feet for levelling
- Above-surface filling with pull-type valve
- FEIGE web HMI as user interface with integrated scale display and operation monitoring
- More than 1000 dosing parameters for different products possible
- Control of on-site product pump or pilot valve is included
- By default with 2 or 3 weighing ranges
- Single point load cell by default in stainless steel design
- With 2g-increment also suitable for filling tins
- Any number of drive units can be controlled
- A non-driven or an electrically driven roller conveyor can be installed on the weigh scale platform
- Matching, complementary product hose available
- Stainless steel and acid-resistant design possible
- Mobile design possible
- ATEX design possible
A wide range for many different types of canisters
Canisters are put to frequent and varied use. Challenges range from sticky to hazardous products where the safety of employees is the primary focus. Overflow messages and ATEX conformity are only two of many requirements that need to be met. A rapid valve change is just as important if different products are filled and unnecessaries standstill is to be avoided.
Mathias Hühn
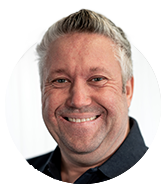
Mathias Hühn
Sales Manager
Semi-automatic
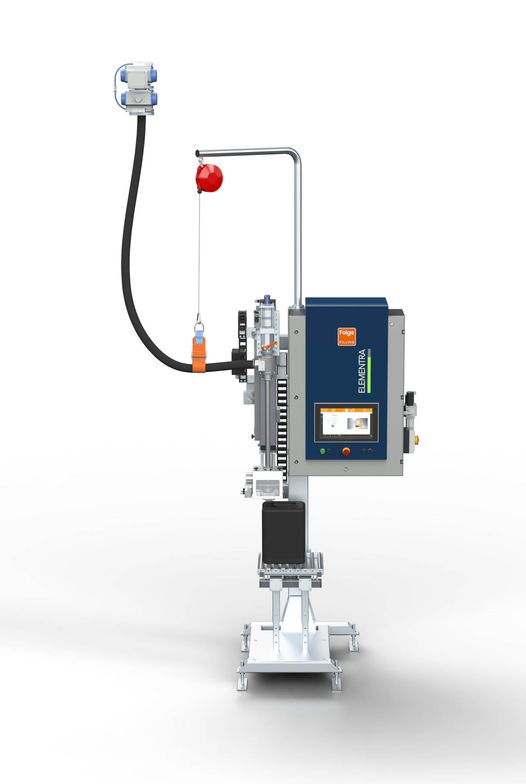
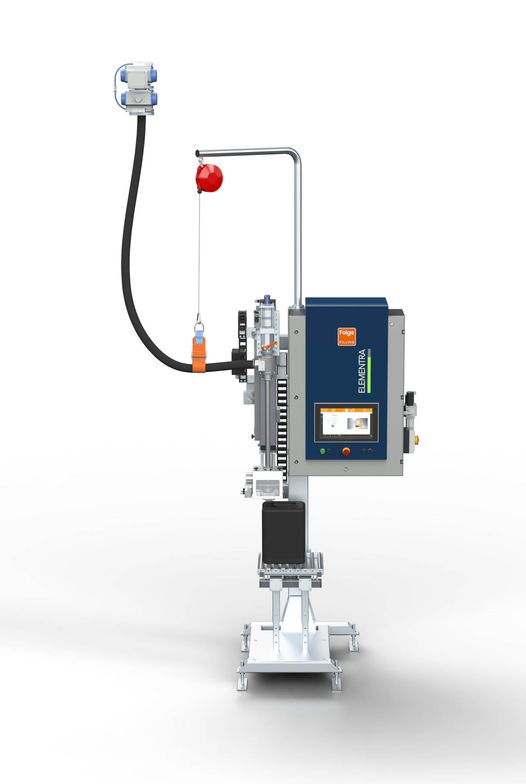
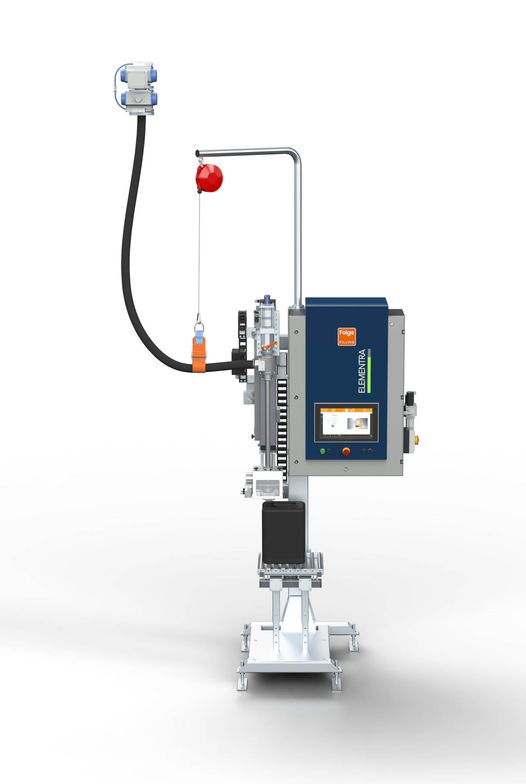
The canister filling equipment ELEMENTRA® 25 is the solution for complex tasks. The semi-automatic equipment can be extended and complemented as desired according to your requirements with the well-proven FEIGE modular system.
Depending on your needs, you can connect conveyor systems and further peripheral components for the in-feed and out-feed area. How the equipment is connected to control systems is specified by you because its interfaces are optionally freely configurable.
The benefits - canister filling equipment ELEMENTRA® 25
- Sturdy basic structure with machine feet for levelling
- Below-surface filling with weight-controlled upward movement or below-bunghole filling
- FEIGE web HMI as user interface with integrated scale display and operation monitoring
- More than 1000 dosing parameters for different products possible
- Control of on-site product pump or pilot valve is included
- By default with 2 or 3 weighing ranges
- Single point load cell by default in stainless steel design
- With 2g-increment also suitable for filling tins
- Any number of drive units can be controlled
- A non-driven or an electrically driven roller conveyor can be installed on the weigh scale platform
- Matching, complementary product hose with hose suspension available
- Stainless steel und acid-resistant design possible
- Mobile design possible
- ATEX design possible
Fully automatic
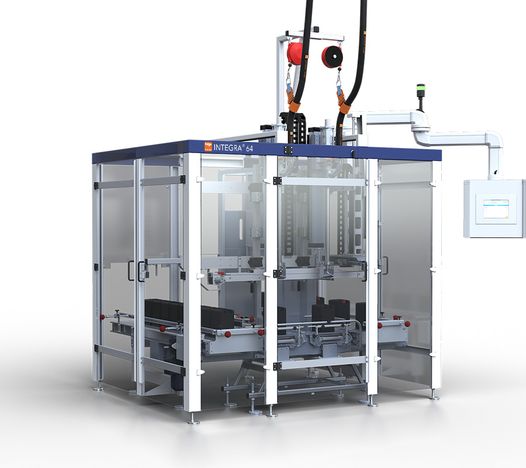
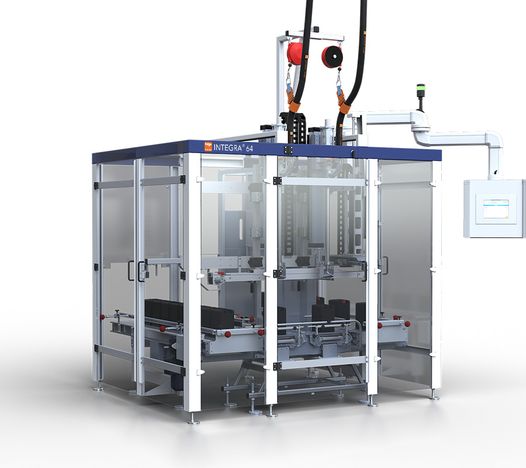
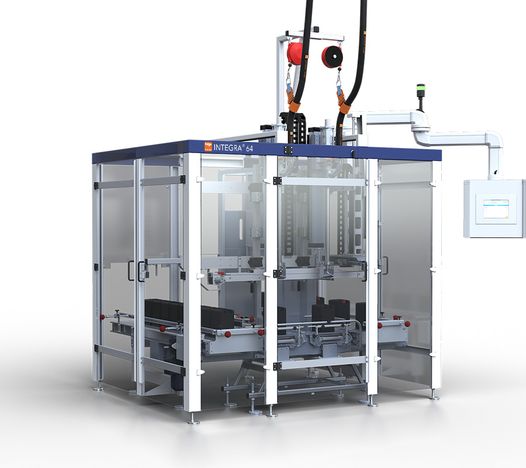
If you want to use a compact, highly-integrated and powerful automatic filler on a small surface, the automatic canister filling machine INTEGRA® 64 is exactly the right choice.
The conveyor system is preferably arranged in U-shape to allow for an ergonomic operation with one operator. Empty canisters and caps or push-in plugs are placed onto the conveyor from one position. The canisters that have been filled with calibrated accuracy and closed are subsequently palletised. To increase the performance, you can complement the automatic filling machine with an in-feed table, cap or push-in plug sorting pot or palletising aid or palletising robot at any time.
The benefits - automatic canister filling machine INTEGRA® 64
- Very cost-effective solution as the complete control and operation are compactly installed on the filling station
- Extension into a filling line possible with conveyor technology and other peripheral components
- Sturdy basic structure with machine feet for levelling
- Easy installation
- FEIGE web HMI as user interface with integrated scale display and operation monitoring
- More than 1000 dosing parameter records for different products possible
- Actuation of on-site product pump or pilot valve is included
- By default with 2 weighing ranges
- Single point load cell by default in stainless steel design
- No checkweigher for pre-packages required
- Matching, complementary product hose available
- Also available in stainless steel design
- Easily expandable for higher performance or automation
- A second filling place can either operate with prefilling and final filling to increase the performance or can alternatively be used for a rapid batch or product change
- Stainless steel and acid-resistant design possible
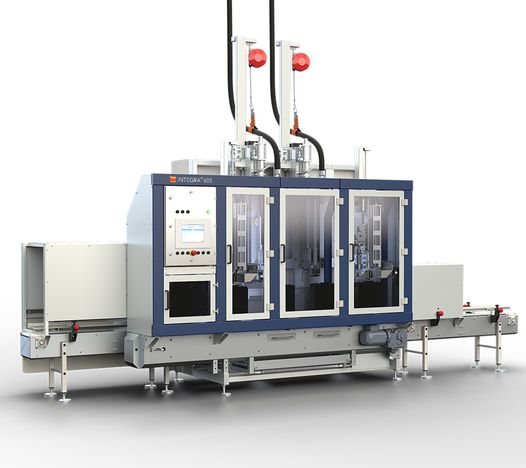
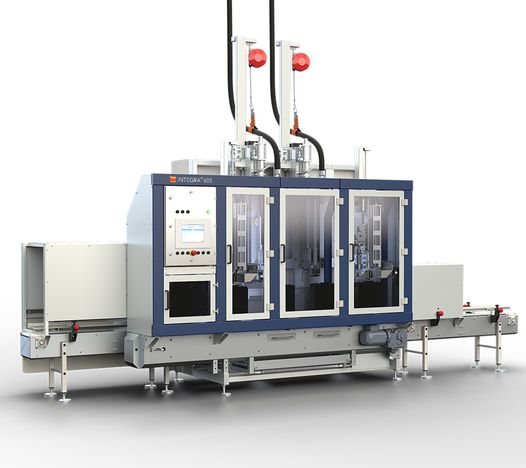
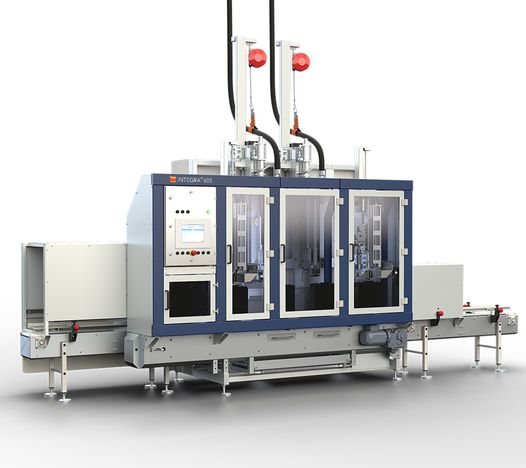
The automatic canister filler INTEGRA® 605 is available to you for filling canisters in below-surface or below-bunghole mode.
Type 605 ideally adapts to your upstream or downstream processes, such as pump actuation, empty canister magazine, labelling and palletising. Fully equipped, type 605 consists of the integrated work stations positioning, opening, pre-filling and final filling and closing.
You specify whether the canisters are fed open, with screw cap or with dust cap and whether they are closed with a push-in plug or a screw cap after filling.
The benefits - automatic canister filler INTEGRA® 605
- Calibrated high-performance filling also in the field of pre-packages
- Extension into a filling line possible with conveyor technology and other peripheral components
- FEIGE web HMI as user interface with integrated scale display and operation monitoring
- More than 1000 dosing parameters for different products possible
- Cyclic monitoring of the filling unit, e.g. mis-alignment protection, tare- and tolerance check, flow rate and fill time monitoring
- Integrated push-bar chain conveyor, the canisters are conveyed under the work station in clocked operation and with millimetric accuracy
- Optional communication and data exchange with on-site control system
- Stainless steel und acid-resistant design possible
- ATEX design possible
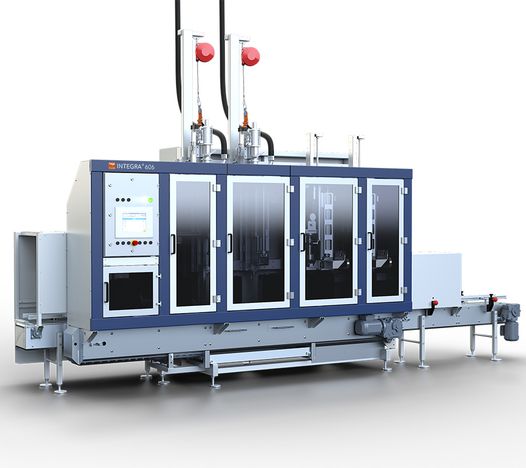
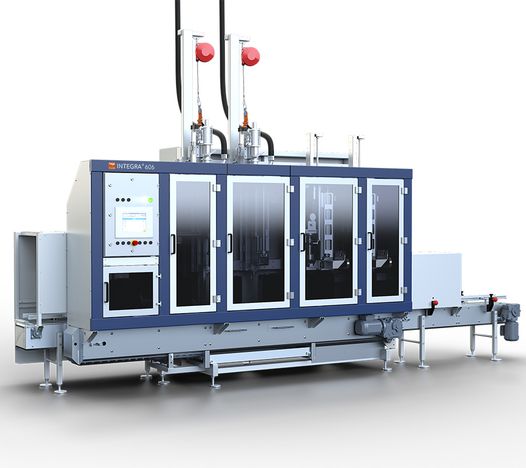
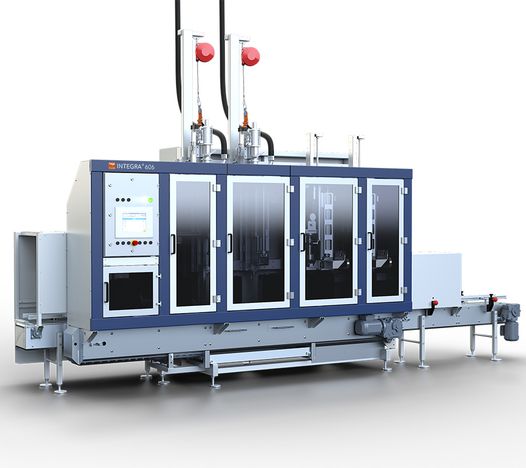
With the automatic canister fillers INTEGRA® 606 and 608 you can increase the filling output once again.
The two machines stand for high-performance filling also in the pre-package field. The model 606 works with 3 double cycle stations, and optionally as model 608 with 4 double cycle stations.
The benefits - automatic canister filler INTEGRA® 606/608
- Calibrated high-performance filling also in the field of pre-packages
- Extension into a filling line possible with conveyor technology and other peripheral components
- FEIGE web HMI as user interface with integrated scale display and operation monitoring
- More than 1000 dosing parameter records for different products possible
- Cyclic monitoring of the filling unit, e.g. mis-alignment protection, tare and tolerance check, flow rate and fill time monitoring
- Integrated push-bar chain conveyor, the canisters are conveyed under the work stations in double cycle with millimetric accuracy
- Optional communication and data exchange with on-site control system
- ATEX design possible
- Stainless steel and acid-resistant design possible